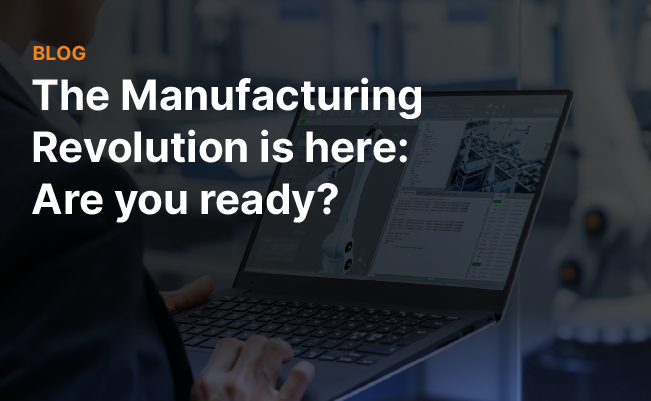
The manufacturing industry has always been driven by efficiency, innovation, and process optimization. But as the sector faces new challenges and opportunities, the conversation is shifting. While technology remains a key enabler of transformation, it’s clear that people, culture, and processes must evolve alongside it. In a recent panel discussion, industry experts Ebrahim Alareqi (Principal Machine Learning Engineer, Incorta), Fabien Duboeuf (Industry Lead, Manufacturing, Google Cloud), and Jan Griffiths (Founder, Gravitas Detroit)shared their perspectives on the forces shaping the future of manufacturing—particularly in the context of AI, data, and cultural change.
The Role of Culture in Manufacturing Transformation
Adopting emerging technologies like AI or machine learning is futile if the underlying processes and organizational culture remain outdated. As Jan emphasized, “There’s no point in applying technology to an outdated process.” The real value of innovation lies in rethinking how we operate before embracing new tools. For manufacturers, this means fundamentally reworking the way they design, manufacture, and deliver products. Without a cultural shift that prioritizes adaptability and forward-thinking, even the most advanced technologies will fall short.
Fabian echoed this sentiment, highlighting that the real challenge often lies in aligning people and processes with technological advancements. “You can’t just implement technology without aligning it with your business priorities,” he explained. Success starts with a clear understanding of why change is necessary and how it aligns with broader business goals.
Overcoming Legacy Systems and Embracing New Technology
One of the most significant obstacles for manufacturers, especially in industries like automotive, is the reliance on legacy systems. While these systems are critical to operations, they are often rigid and disconnected, making it difficult to harness the full potential of new technologies. Integrating these systems to enable seamless data sharing remains a pervasive challenge.
Ebrahim shared his experience from his time at Volvo Cars, where integrating legacy systems was a significant hurdle. “For a long time, we focused on the algorithms, but the real challenge was getting all the systems integrated so that the data could flow seamlessly,” he explained. Without a unified data infrastructure, manufacturers struggle to leverage new technologies effectively, hindering their ability to innovate and compete.
Generative AI: A Catalyst for Change
GenAI has emerged as a game-changer in the manufacturing world. Fabian Dubuff discussed how AI can help solve the problem of disparate data by enabling manufacturers to quickly access insights—even from legacy systems. The goal, he explained, is to create an ecosystem where employees can retrieve the information they need without being bogged down by the complexities of underlying systems.
AI should not be seen in isolation. Instead, it must be integrated into the broader manufacturing ecosystem to bridge gaps in the supply chain, streamline operations, and optimize customer experiences. “The future of manufacturing lies in combining cutting-edge technology with a culture of innovation that allows companies to be more agile and responsive,” Jan added.
The Power of “What-If” Scenarios
AI and data analytics push manufacturers to explore “what-if” scenarios, which can predict and respond to disruptions before they occur. Fabian posed the question, “What if there’s a strike in Mexico or a regulatory change in Europe?” Simulating different scenarios in real-time is a game-changer, allowing manufacturers to make faster, more informed decisions and stay ahead of the curve in an increasingly volatile environment.
Building Trust in Data and Technology
While technology is powerful, its success depends on the trust of the people who use it. Ebrahim emphasized that one of the biggest challenges with new technologies, especially AI, is overcoming skepticism among employees. “We have to make sure that employees can rely on the data they’re using,” he explained. Ensuring that data is clean, accessible, and trustworthy is critical to fostering this trust.
Whether it’s making decisions on the shop floor or negotiating with suppliers, having accurate, real-time data is essential. For many manufacturers, this means breaking down data silos and integrating information across systems to create a single source of truth. Only then can organizations fully leverage the potential of their data and technology investments.
Starting Small and Scaling Up
A common theme in the discussion was the importance of starting small when implementing new technologies. Focusing on small, high-impact projects and gradually scaling them up ensures that new technology is tested and trusted before being rolled out across the organization.
Fabian agreed, stressing the importance of defining clear business priorities before deploying technology. “You have to start with a vision and then scale quickly,” he advised. By aligning technology deployments with business goals, manufacturers can ensure that their investments deliver meaningful results.
The Road Ahead: Embracing Complexity
The future of manufacturing will require organizations to embrace complexity and change. As Fabian warned, “If you don’t embrace complexity, your competition will.” Digital-native companies, unburdened by legacy systems, are setting new standards for agility and innovation. For traditional manufacturers, this presents both a challenge and an opportunity. By understanding the complexities of modern manufacturing and using technology to their advantage, manufacturers can unlock new levels of efficiency and competitiveness. The key lies in combining cutting-edge tools with a culture that embraces change and innovation.
The future of manufacturing will not be defined by technology alone. It will be shaped by the ability of organizations to adapt their culture, processes, and people to the demands of the modern world. By embracing AI, leveraging real-time data, and starting with small but impactful projects, manufacturers can position themselves for success in the years ahead.
Want to learn more? Check out the full discussion on demand.